Blister Packing: Types, Materials & Production
In the pharmaceutical industry, blister packaging is vital, especially when making tablets. It offers a safe and practical packaging solution that guarantees the tablets' integrity, safety, and effectiveness throughout their shelf life.
The usage of a blister pack, which has discrete cavities or compartments that house each tablet, is blister packaging for tablets.
These compartments are frequently composed of plastic, such as PVC or PET, and are covered with foil or a lidding material to keep out air and moisture.
The blister pack is made to shield the tablets from elements like moisture, light, and air that could harm them and reduce their efficiency.
There are various processes involved in the blister packaging procedure for making tablets. The tablets are first put into the compartments of the pre-formed blister packaging.
After that, an aluminum-based foil or lidding substance is used to close the blister pack. The sealing procedure guarantees the packaging's integrity and tamper-evident status. The blister packs can then be packaged for delivery in cartons with labels on them.
In tablet manufacturing, blister packaging has a number of benefits. It offers individual unit-dose packaging so that patients can easily identify themselves and maintain dosage control.
Blister packs are always transparent. This advantage makes it possible to visually verify the pills, confirming the quality and authenticity of the drugs. Patients may simply keep track of their drug intake, which helps with medication adherence.
Blister packaging also increases the productivity of pharmaceutical manufacturers by enabling automated packing procedures and lowering the possibility of human error.
Six Types of Blister Packaging in Tablets
There are many types of blister packaging used in tablets. The following are the most popular ones.
● Push-through Blister Packs
In this type of blister packaging, each tablet is individually sealed in a separate cavity. The back of the blister pack is made of aluminum foil or a laminate, which can be easily pushed through to access the tablet.
● Cold-form Blister Packs
Cold-form blister packaging is commonly used for moisture-sensitive tablets. It involves the use of aluminum foil that is formed around the tablet, providing excellent protection against moisture and extending shelf life.
● Thermoformed Blister Packs
Thermoformed blister packaging is created by heating a plastic sheet, typically PVC or PET, and forming it into cavities that hold the tablets.
The blister is then sealed with a lidding material, such as aluminum foil or laminate.
● Child-resistant Blister Packs
Child-resistant blister packaging is designed to prevent children from accessing the tablets. It incorporates additional features, such as special locking mechanisms or complex opening instructions, to ensure safety.
● Peel-off Blister Packs
Peel-off blister packaging allows users to easily peel back the foil or lidding material to access the tablet. This type of packaging provides convenience and is commonly used for over-the-counter medications.
● Calendar Blister Packs
Calendar blister packaging includes multiple cavities arranged in a calendar-like format, with each cavity representing a specific day or dosage. This type of packaging is commonly used for medications that require strict dosage schedules.
These are some of the common types of blister packaging used for tablets. The selection of the appropriate type depends on factors such as product requirements, dosage form, regulatory compliance, patient convenience, and industry standards.
Six Materials Used in Blister Packaging for Tablets
1. PVC (Polyvinyl Chloride): PVC is a commonly used material in blister packaging for tablets. It provides excellent clarity, allowing visibility of the tablets inside the blister.
PVC offers good barrier properties against moisture, light, and oxygen, protecting the tablets from degradation. It is also known for its formability, making it suitable for thermoforming processes.
2. PVDC (Polyvinylidene Chloride): PVDC is often used as a coating material for blister packaging. It provides enhanced barrier properties, particularly against moisture and oxygen. PVDC-coated films are commonly used as lidding materials to seal the blister packs.
3. PET (Polyethylene Terephthalate): PET is a transparent and lightweight material that offers good mechanical strength and chemical resistance.
It is used for both the blister and lidding materials in blister packaging. PET provides excellent moisture and gas barrier properties, ensuring the stability and integrity of the tablets.
4. COC (Cyclic Olefin Copolymer): COC is a relatively new material used in blister packaging. It offers high clarity, good barrier properties, and chemical resistance. COC films provide excellent moisture and gas barrier, protecting the tablets from external factors.
5. Aluminum Foil: Aluminum foil is commonly used as a lidding material in blister packaging. It offers excellent barrier properties against moisture, oxygen, and light. Aluminum foil provides a tamper-evident seal and ensures the integrity and stability of the tablets.
6. Paperboard: Paperboard materials are sometimes used as the backing cards for blister packaging. They provide structural support, branding opportunities, and can be printed with important product information.
The selection of the material depends on various factors, including the specific requirements of the tablets, regulatory compliance, product stability, and the desired level of protection. It is important to consider the compatibility of the material with the tablets, ensuring that it does not interact or compromise the quality of the medication.
Blister Packaging Equipment and Machinery for Tablet Production
Blister packaging equipment and machinery are used to make packages for tablets. These machines have different parts and functions.
They can form the blister cavities, fill the tablets into the cavities, and seal the blisters with a protective cover.
The machines are operated by experts who make sure everything works properly. These machines help in packaging tablets quickly and accurately, making sure they are safe and protected.
Let’s quickly examine how some of the Blister Packaging Machines work.
Automatic Aluminum-Plastic Blister Packaging Machine DPP-140
With its advanced features and user-friendly design, this machine ensures top-quality results every time.
One of the key features is the gear motor, which powers the main shaft for smooth and consistent operation. Controlled by the PLC system, the machine achieves precise mechanical motion for optimal performance.
The forming mechanism, driven by a cam, creates perfectly shaped blisters, while the heat-sealing mechanism, operated by the cylinder, securely seals the blisters with PVC and aluminum foil. The process is simple yet effective.
The DPP-140 machine is designed to meet various packaging needs. It can handle a wide range of products, including capsules, tablets, sugar-coated tablets, and ampoules.
With its excellent sealing performance and attractive appearance, your products will stand out in the market while maintaining the highest standards of safety and hygiene.
You need to get the DPP-140 Blister Packaging Machine and experience the difference in efficiency, quality, and customer satisfaction.
Boost your production capabilities and gain a competitive edge with this reliable and versatile packaging solution.
Automatic Blister Packing Machine DPP-88
Another great blister packaging equipment and machinery for tablet production is the Automatic Blister Packing Machine DPP-88.
One of the standout features of the DPP-88 is its exceptional build quality. The key parts are constructed using stainless steel and high-grade aluminum alloy, ensuring durability and reliability.
This machine is perfectly suited for various industries, including pharmaceuticals, food, and health products. Whether you need to package tablets, capsules, small food items, or even hardware parts and electronic components, the DPP-88 can handle it all.
This versatile machine integrates ten essential functions, streamlining your packaging process. From coiled material uncoiling to aluminum and plastic feeding, blister forming, filling, waste material recycling, heat sealing, batch number printing, reticulate indentation, sheet blanking, and finished product counting, the DPP-88 ensures a seamless and efficient packaging operation.
With its advanced technology and adherence to GMP standards, the DPP-88 has gained recognition and trust from major pharmaceutical factories and large hospitals both domestically and internationally. Its exceptional performance and reliability have made it a popular choice in over 20 countries and regions worldwide.
When you choose the DPP-88, you can expect well-sealed, safe, and hygienic packaging for your products. Say goodbye to concerns about product integrity and enjoy peace of mind knowing that your items are securely packaged and ready for distribution.
Get the Automatic Blister Packing Machine DPP-88 and experience the difference it can make in your packaging process.
Increase efficiency, enhance product safety, and gain a competitive edge in the market. Join our satisfied customers who have chosen the DPP-88 as their go-to packaging solution.
Don't miss out on this opportunity to take your business to new heights. Contact us today to place your order and start enjoying the benefits of the DPP-88!
Seven Steps in the Blister Packaging Process for Tablets
The blister packaging process for tablets typically involves the following steps:
1. Material Preparation: The materials required for blister packaging, such as PVC (Polyvinyl Chloride) or PVDC (Polyvinylidene Chloride) film and aluminum foil, are prepared and made ready for use.
2. Forming the Blisters: The PVC film is fed into the blister packaging machine, where it undergoes heating and forming processes. Compressed air is used to shape the PVC film into individual pockets or cavities, creating the blister packs that will hold the tablets.
3. Filling the Blister Packs: Once the blister packs are formed, the next step is to fill them with the tablets. This can be done manually or using automated systems, depending on the scale of production.
4. Sealing the Blister Packs: After the tablets are placed in the blister packs, the packs are covered with aluminum foil. Heat and pressure are applied to seal the aluminum foil to the blister packs, ensuring the tablets are securely enclosed.
5. Quality Control: The sealed blister packs undergo rigorous quality control checks to ensure they meet the required standards. This includes checking for proper sealing, accurate tablet placement, and overall packaging integrity.
6. Printing and Labeling: Batch numbers, expiration dates, and other necessary information are printed on the blister packs. Labels may also be applied, providing additional information and branding.
7. Packaging and Storage: The sealed and labeled blister packs are then packaged in appropriate containers, such as boxes or cartons, ready for storage or distribution.
It's vital to remember that the specific procedures may differ according to the tools and technology employed, the demands of the pharmaceutical company, or legal restrictions.
Summary
Blister packaging ensures safe and convenient tablet packaging. It protects tablets from moisture, light, and air, preserving their effectiveness.
Different types of blister packs are available, including push-through, cold-form, and thermoformed packs. Materials like PVC, PVDC, PET, COC, and aluminum foil are used.
Blister packaging machines like DPP-140 and DPP-88 streamline the process. Steps include material preparation, forming the blisters, filling, sealing, quality control, printing, and packaging.
Blister packaging enhances production and product safety, offering a competitive advantage.
Leave your comment
Also Offers


Containment Automatic Capsule Filling Machine SFK-703

Fully Automatic Dosator Capsule Filling Machine CZ-40

Our Team
As an expert in the pharmaceutical and pharmaceutical packaging industry, iPharMachine has provided solutions for hundreds of pharmaceutical and health product manufacturers for 17 years. By visiting customers, we get good reviews from our customers.
- info@ipharmachine.com
- English Español Deutsche
Recently viewed
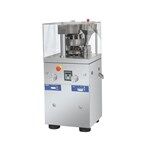